Mengintip Proses Produksi Ban Hankook, Mengandalkan Otomasi dan Teknologi Canggih
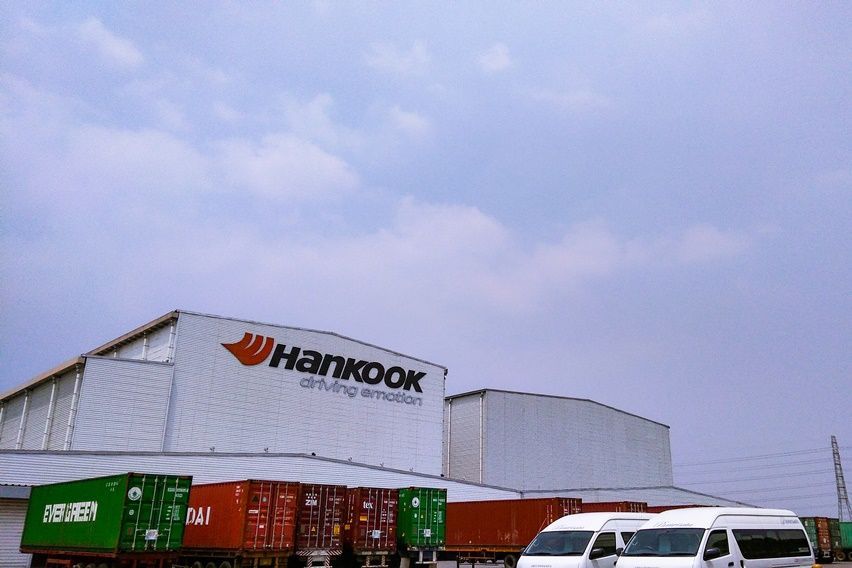
Hankook Tire Indonesia Plant di Cikarang, mampu memproduksi sekitar 30 ribu ban per hari. Jika diakumulasi selama setahun, jumlahnya memukau. Lebih dari 11 juta ban sanggup mereka distribusikan ke seluruh dunia dari satu pabrik di Indonesia. Itulah kesan dari kunjungan media yang dihelat pabrik ban asal Korea Selatan ini. Selama kunjungan kami berkesempatan melihat langsung proses produksi di pabrik serbaotomatis dan canggih ini.
Pengolahan Bahan Baku
Proses pembuatan ban diawali dengan pencampuran bahan dasar karet dengan bermacam bahan kimia. Hankook menggunakan dua jenis karet, natural dan sintetis. Porsi dari seluruh ban yang diproduksi, 55% menggunakan jenis natural sementara sisanya sintetis.
Output pengolahan bahan dasar berupa lembaran karet panjang. Material utama dikirimkan menuju tiga lini produksi: extrusion, bead dan calendering. Extrusion menekan beberapa lembaran karet menjadi satu, yang nantinya menjadi bagian telapak ban. Proses bead menyambungkan kawat baja berlapis tembaga menjadi sebuah bentuk lingkaran. Setelah dibalur karet, komponen ini membentuk profil samping ban yang menggigit bibir pelek. Selanjutnya calendering menghasilkan komponen, yang tugasnya menjaga postur ban (inner lining). Gulungan kain atau kawat besi khusus diapit lembaran karet seperti sandwich, kemudian dipres. Lantas dipotong sesuai ukuran yang dibutuhkan.
Selama kunjungan pabrik, tidak banyak operator yang bergerak kesana kemari. Mayoritas pengolahan material hanya butuh pengawasan operator. Fitur Material Check menggunakan RFID dan barcode, memastikan penggunaan material sesuai dengan produk yang dihasilkan. Penting menggunakan fitur ini, sebab lebih dari seribu jenis item berbeda diproduksi Hankook di Indonesia.
Assembling
Ketiga komponen kembali diarahkan menjadi satu garis produksi. Pada mesin perakitan yang cukup besar, Inner lining masuk terlebih dahulu menuju silinder berputar yang disebut carcass drum. Operator menyelaraskan sisi terluarnya sesuai arahan laser. Ia juga menempatkan bead di bagian 'tangan' mesin produksi. Setelah semua sesuai posisi, mesin bekerja secara otomatis. Tidak sampai satu menit sebuah green tire selesai dirakit. Green tire merupakan produk yang berbentuk ban namun belum terdapat garis telapak maupun detil pada dinding samping. Masih perlu 'dimasak' pada tahap curing.
Sebelum memasuki proses selanjutnya, green tire disimpan rapi di rak besar nan tinggi. Dua robot bertugas menyimpan stok dan mengirim ke lokasi proses selanjutnya. Penyimpanan ini membantu mengurangi human error dan mempermudah pembagian kerja mesin.
Finishing, Kontrol Kualitas, dan Gudang Penyimpanan
Rel di bagian langit-langit mengirim setiap ‘ban mentah’ sesuai tujuan mesin curing. Selama proses pematangan, ban dipanaskan dalam sebuah cetakan yang membentuk patron telapak serta dindingnya. Uap sepanas 207 derajat Celcius menyembur selama 15-20 menit. Melenturkan material karet demi kesempurnaan proses pencetakan. Begitu selesai, gas nitrogen mempercepat proses pendinginan, menghindari terjadinya deformasi.
Ban hasil proses curing masih perlu dicukur (trimming). Di sini tangan manusia diperlukan. Sebab tidak sekadar mencukur, operator bertugas menginspeksi secara visual. Mengidentifikasi cacat produk yang tampak. Pun sebelum bisa masuk gudang, ban masih harus dicek kualitasnya. Perangkat yang disebut Tire Uniformity Check menjadi penjaga pintu gudang. Memastikan hanya produk sempurna yang berhak memasuki gudang.
Tire Uniformity Check bertugas menguji keselarasan dan keseimbangan ban. Supaya lolos, permukaan ban harus rata tanpa benjolan. Keseimbangan rotasi ban juga diuji. Tidak boleh ada bobot yang lebih berat di satu titik demi menjamin keselamatan dan kenyamanan berkendara.
Pergerakan produk setelah proses QC, dilakukan sepenuhnya menggunakan fitur automatic storage. Tangan robot besar bergerak sesuai koordinat yang ditentukan. Ban ditumpuk satu per satu sesuai jenisnya. Kemudian memindahkan satu tumpukan tersebut ke conveyor belt menuju gudang penyimpanan.
Dalam satu hari, Hankook sanggup menghasilkan sekitar 30 ribu ban baru. Kapasitas produksi sebanyak 12 juta ban per tahun diutamakan untuk suplai pasar global. Sebanyak 92% dikirim ke luar negeri. Berbagai merek ternama mempercayakan ban asal Korea Selatan ini. Sebut saja Porsche, Mercedes dan BMW. Maka dari itu, quality control berperan penting.
Ada lima kategori ban yang diproduksi dalam fasilitas pabrik seluas 600.000 m2 ini. Standard Performance, High Performance, Ultra High Performance, LTR SUV dan LTR Van. Perbedaan terletak pada fungsi serta material compound yang digunakan. Banyaknya ragam produk terbukti saat melongok gudang penyimpanan. Kami melihat berbagai nama seperti Hankook Kinergy EX, Winter i*Pike khusus salju, hingga Laufenn dengan speed rating W (kecepatan maksimum 280 km/jam). (Krm/Odi)
Baca Juga: Pameran Mobil Klasik Concours d’Elegance Digelar di Indonesia
Jual mobil anda dengan harga terbaik


GIIAS 2024
IMOS 2024
Tren & Pembaruan Terbaru
- Terbaru
- Populer
Anda mungkin juga tertarik
- Berita
- Artikel feature
Mobil Pilihan
- Terbaru
- Yang Akan Datang
- Populer
Video Mobil Terbaru di Oto
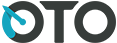
Artikel Mobil dari Carvaganza
Artikel Mobil dari Zigwheels
- Motovaganza
- Tips
- Review
- Artikel Feature
- advice