Mengintip Proses Kelahiran Mobil Toyota
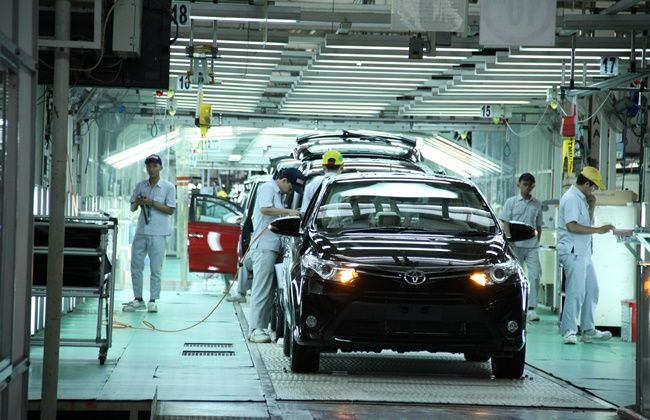
Perlu waktu enam bulan bagi Toyota Motor Manufacturing Indonesia (TMMIN), menyiapkan lini produksi sebuah mobil yang benar-benar baru. Itu pun di luar waktu yang diperlukan untuk survey kebutuhan pasar. Tapi hal itu bukanlah poin utama yang ingin kami sampaikan, namun bagaimana sebuah mobil bisa terwujud.
Beruntung bagi kami karena pihak TMMIN mengundang untuk mengunjungi fasilitas mereka di Karawang, Jawa Barat. Tepatnya Karawang Plant 2, yang lini produksinya menghasilkan Toyota Sienta, Etios Valco, Yaris dan juga Vios/Limo. Mobil-mobil ini kemudian diproduksi untuk pasar ekspor maupun domestik.
Di tempat ini, selembar plat baja akan bertransformasi dalam waktu 22 hingga 24 jam menjadi sebuah mobil yang akan mengisi garasi rumah Anda. Proses pembuatan yang rumit, canggih dan membutuhkan ribuan tenaga kerja. Kemudian dukungan ribuan suplier dalam dan luar negeri, diperlukan untuk membuat satu unit mobil.
Ada banyak hal yang dapat dilihat di tempat ini. Pertama standar tinggi Toyota, kedua bagaimana seorang karyawannya didorong selalu berkreasi, untuk menciptakan inovasi yang menunjang proses kerja mereka. Dan yang terakhir, produk anti- karat after market ternyata benar-benar tidak penting.
Press Shop: Dari 2 Dimensi Jadi 3 Dimensi
Departemen pertama yang kami masuki adalah bagian pressing atau pencetakan komponen bodi. Di tempat inilah proses kelahiran sebuah mobil dimulai. Pada prosesnya, baja yang datang dari Jepang, Korea dan Cilegon dibentuk dengan mesin berkekuatan puluhan ton hingga menjadi pintu, atap, kap mesin, panel body termasuk chassis. Untuk bagian-bagian yang memiliki dimensi lebih kecil, press shop di pabrik Toyota Sunter lalu kemudian dikirim ke Karawang.
Setiap komponen yang selesai dipress, menjalani inspeksi menyeluruh. Gunanya untuk memastikan semuanya sesuai dengan standar kualitas yang berlaku. Meski demikian, ada saja part yang mengalami defect atau cacat. Parts seperti ini biasanya di-recycle atau dibuang kalau memang sudah tidak bisa diperbaiki.
Welding Shop: Proses menjahit mobil
Pengelasan menjadi metode untuk menyatukan semua barang yang dikirim dari tempat pressing tadi. Upper dan lower body dijadikan satu menggunakan las titik yang dioperasikan oleh pekerja maupun robot.
Menurut keterangan TMMIN, sebuah mobil Toyota biasanya memiliki sekitar 3.000 titik pengelasan. Yang menarik, tidak semua bagian dilas untuk dijadikan satu. Teknologi terbaru yang dimiliki TMMIN adalah roller hemming. Inilah alat yang menyatukan outer dengan inner panel.
Contoh paling sederhana, kalau Anda perhatikan pintu mobil, di pinggiran pintu ada bagian yang seperti tertekuk dan menyatu dengan bagian dalam pintu. Nah inilah yang disebut hemming. Teknologi lainnya yang terbilang baru adalah yang disebut sebagai spot piano, yang berfungsi menyatukan bagian outer dan inner atap.
Disebut sebagai spot piano karena alatnya memang mirip dengan tuts alat musik tekan yang akan menggerakan alat las titik. Dengan pemrograman yang telah dilakukan sebelumnya, alat ini sudah mengerti mana yang harus mengelas di kedua sisi.
Alat ini bukan dibuat oleh seorang engineer dari negeri antah berantah. Tapi asli hasil pemikiran seseorang bernama Warisno. Veteran Karawang Plant 2 yang telah mengabdi selama 13 tahun. Sebelum Warisno yang menjabat sebagai team leader di Departemen Welding menemukan ide ini, ia dan timnya harus bergerak mengelilingi atap untuk mengelas. Alhasil, selain melelahkan, prosesnya memakan waktu.
Paint Shop: Siapa Butuh Anti Karat?
Inilah pertama kalinya TMMIN membukakan pintu kepada ‘orang luar’, untuk melongok seperti apa proses pengecatan mereka. Cat yang digunakan juga diklaim ramah lingkungan karena memiliki basis air (water based paint). Mobil yang baru selesai dilas, kemudian berjalan melalui semacam conveyor, melewati berbagai cairan untuk membersihkannya dari kotoran sisa pengelasan.
Entah berapa banyak langkah pembersihan ini. Yang jelas sebuah mobil harus melewati 12 proses hingga akhirnya keluar dari pengecatan. Tapi ada dua hal yang menarik perhatian kami. Pertama adalah Bazooka System, di mana mobil disemprot dengan air sebanyak 1.500 liter per menit. Di sinilah residu pengelasan dibersihkan.
Kedua pemasangan lapisan anti-karat. Cangkang mobil yang bergerak kemudian dicelupkan ke dalam cairan anti-karat tidak kurang dari tiga menit. Dengan demikian, semua bagian dijamin akan terlapisi. Pertanyaan kemudian muncul: kalau begitu apa gunanya lapisan anti-karat after market itu?
Ke tempat ini pun prosesnya lumayan ‘ribet’. Selain sepatu yang harus dibungkus, mantel khusus juga wajib dikenakan. Bahkan sebelum masuk semua partikel debu di pakaian dibersihkan dengan blower khusus. Selesai? Belum. Semua harus mencuci tangan. Proses yang panjang ini dibutuhkan agar ruang pengecatan tetap bersih dari partikel debu yang bisa terbang menempel pada body yang akan dicat.
Final Assembly
Sebuah mobil menjadi lengkap di tempat ini dengan pemasangan peranti pendukung seperti jok, dashboard, stir, kelistrikan, mesin dan sebagainya. Di ujung lini final assembly inilah mobil untuk pertama kalinya dihidupkan dan melakukan perjalanan pertamanya sejauh kurang lebih 10 meter menuju tempat final inspection.
Satu hal yang menarik di final assembly ini adalah banyaknya terobosan yang dilakukan oleh karyawan TMMIN, untuk mendukung proses kerja yang efisien. Terobosan ini disebut sebagai karakuri.
Beberapa karyawan asli TMMIN berhasil menciptakan alat yang tidak hanya memudahkan mereka bekerja, tapi juga membawa efisiensi waktu proses pemasangan. Menurut keterangan tertulis TMMIN, ada 297 alat hasil karakuri yang semuanya merupakan buah pemikiran karyawan TMMIN.
Baca Juga: Toyota Indonesia perluas pangsa ekspor
Jual mobil anda dengan harga terbaik


GIIAS 2024
IMOS 2024
Tren & Pembaruan Terbaru
- Terbaru
- Populer
Anda mungkin juga tertarik
- Berita
- Artikel feature
Mobil Pilihan
- Terbaru
- Yang Akan Datang
- Populer
Video Mobil Terbaru di Oto
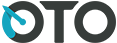
Artikel Mobil dari Carvaganza
Artikel Mobil dari Zigwheels
- Motovaganza
- Tips
- Review
- Artikel Feature
- advice